Look for the green tag
Ask Susan Sandberg, RN, whether the new Equipment Depot at VGH will benefit patients and staff and she’ll tell you it already has.
“Just the other week we had a Code Blue — a cardiac arrest —and we needed an IV pump. In the past, we would have had to strip another patient of a pump — and clean it — before we got the equipment to the patient in distress,” says the clinical educator on unit T8. “But this time it was easy; we just ran to the unit’s Clean Supply Room and got another pump.”
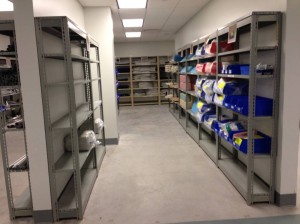
…and the Equipment Depot after.
As part of the hospital’s efforts to prevent C. difficile infections (CDIs), the CDI Working Group linked arms with Inventory Replenishment to establish the new and improved Equipment Depot located in the basement of VGH. Previously cluttered by surplus equipment (some of which we’ve donated to Libya), the space is now pristine and clutter-free. Just the kind of place you’d want your equipment to come from. And, thanks to the hospital’s new process for cleaning and distributing mobile biomedical equipment from the depot, staff can provide faster and better care to patients.
“It gives me peace of mind knowing that clean equipment will be there when we need it and there won’t be any delay in the patient’s therapy,” Susan says.
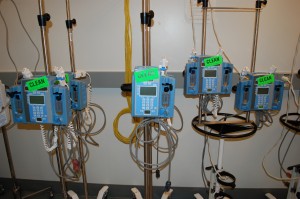
IV pumps with the green tag of confirmation that they are ready for use.
If it’s green, it’s clean
In February, 15 VGH patients acquired C. difficile — that’s 12 fewer patients than in January — and Sydney Scharf, co-lead of the CDI Initiative, is confident we’ll continue moving in the right direction.
“Now that we’ve improved the way mobile biomedical equipment travels between units and the Equipment Depot, we have one more critical component in our overall strategy to decrease CDIs,” says in the infection control practitioner.
The new process reduces an equipment’s travel path from seven to just three points of contact, reducing opportunities for cross-contamination and ensuring clean equipment reaches units faster. Each piece of equipment has its own ‘parking spot’ in a unit’s Clean Supply Room, which is regularly re-stocked — no more paging to order equipment.
And, every clean piece of equipment has a bright green tag affixed to it, assuring staff the item is safe, clean and ready to use. “If you see a green tag, it’s safe to use – it’s a promise, a sign of accountability,” says Sydney.
The difference is night and day, adds Susan. “Nurses had to go on a bit of a scavenger hunt to find equipment before. It could take up to a couple of hours to find the equipment you’re looking for or wait for it to be delivered. Today it’s a matter of minutes; you see the green tag and that’s it.”
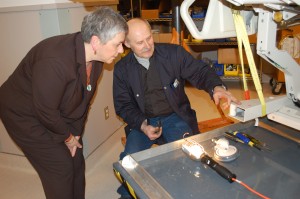
Vic Krzysiek, machinist and millwright, shows Vivian Eliopoulos, executive director for Vancouver Acute, how a new lift table helps him repair beds thoroughly and safely.
Faster, safer bed repairs
But what if a bed needs repairs? The team’s got that covered, too. Down the hall from the Equipment Depot is another spotless room now outfitted with three bays where staff can efficiently – and safely – repair stretchers and beds.
Wieslaw (a.k.a. Vic) Krzysiek, a machinist and millwright, is one of those staff. “This will make my job much easier,” he says with excitement. “We’re better organized here and the new lift tables let me catch issues that would be difficult to see before.”
“Before, we were fixing beds and stretchers in two or three different spots around the hospital and sometimes outside the hospital,” says Brent Corey, maintenance supervisor. The new maintenance room has made it possible for staff to reduce the turnaround on repairs from two to three days to just one.
“The shop’s designed to make things more efficient but also to make things safer for staff,” he adds. “For guys like Vic, we designed the room with ergonomics in mind – with lift tables, a better layout and safer angles for them to work at. So patients and staff are all going to benefit from this.”
Watch for more stories on how VGH staff and our partners are helping us provide best care and prevent hospital-acquired CDIs.