Keeping surgeries sanitized
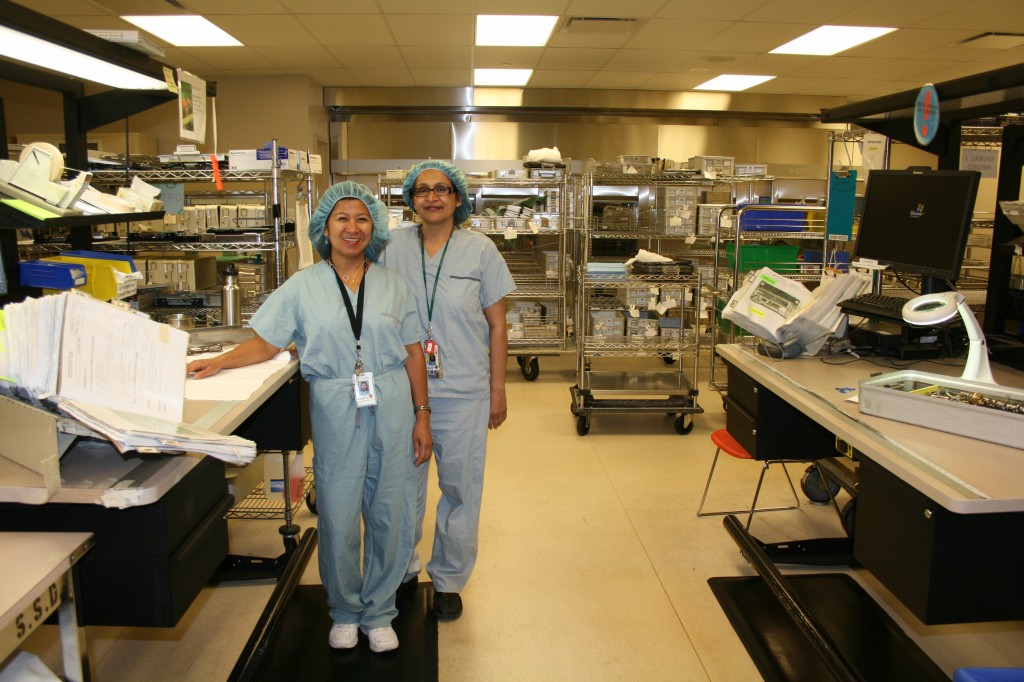
Senior equipment techs Marieta Cheverton (left) and Disho Jakhar (right) document thousands of new medical instruments every year.
In the labyrinthine depths of Vancouver General Hospital, a team of more than 140 people is working 24/7, cleaning, sterilizing hundreds of instruments needed for life-saving surgeries every day.
Like the hearts their instruments help fix, the medical device reprocessing department (MDRD) is a complex, essential component of the bigger picture, providing what is needed for the rest of the hospital as well as other centres around VCH. Sixty five per cent of the instruments come from the operating rooms upstairs and the rest are from other areas of the hospital, from 14 community clinics and facilities such as George Pearson and G.F. Strong and from other locations like UBC Hospital and Lions Gate – it’s the largest department of its kind in B.C. and the third largest in Canada.
“We’re working all the time because as a hospital, as a health care authority, we can’t provide care without sterilized equipment and instruments,” says Albert Csapo, master juggler and manager of the MDRD. “We have such an amazing team here who make it all work and keep things going.”
And part of this team are long-term members Marieta Cheverton and Disho Jakhar, senior equipment technicians in the department. Armed with a camera and meticulous attention to detail, the pair catalogues and photographs any new instruments that come to the hospital on a daily basis.
“We’re kind of the core of the hospital,” says Disho. “Everyone depends on us to get them the sterile items; what they need for surgery or care on their ward.”
Marieta nods in agreement.
“Yeah, you need to make sure they have everything that is needed for the care,” she adds. “Everything needs to be sterile and cleaned and put together properly. It has to be perfect.”
Four phases of reprocessing
To ensure that their work is perfect, the MDRD processes instruments in four phases:
- The instrument go into the decontamination area where the staff take apart the items and give them a thorough pre-cleaning before placing them on carts and rolling them into the five “oversized washing machines.” (Delicate instruments are placed in an ultrasonic machine; power tools are hand washed.)
- After being washed and disinfected, the instruments make their way to the 11 assembly tables where, under bright lights and a magnifying glass, technicians check for cleanliness and functionality before reassembling the items. The technicians have online instructions as well as massive hard-copy manuals to guide the assembly.
- Once they are carefully put back together, the instruments are taken to the sterilizing area where they are subjected to steam at 132 degrees Celsius; the sterilization cycle that takes 90 minutes and kills all microorganisms. It takes at least 60 mins for the items to cool to room temperature before they can be stored without the chance of contamination. Any delicate items are put into the ETO sterilizer, which uses ethylene oxide gas and this sterilization cycle takes a lot longer – 15 hours in total.
- After they cool down, items are moved to the sterile storage areas and can then be distributed to the OR, departments, clinics and off-site facilities to be used again by doctors and nurses.
Complex process
Because there are several areas with a specific focus, Albert has his department divided up into five teams that are dedicated to specific stages in the process like operating the sterilizer or coordinating the items up at the OR.
“There’s so much information and systems to know,” Albert says, shaking his head. “It would be great if everyone was proficient in everything, but it’s impossible. We worked out that if they spent a week at each job, it would take about six months to rotate through.”
To make the process more efficient, Albert and the department are utilizing an online catalogue system, like a library book search, where healthcare professionals can perform instrument searches, bringing up a photo and important information on the item.
“We have a person constantly coordinating and talking to the doctors upstairs about what they need,” Albert says pointing to a screen showing the various schedules of surgeries that day. “This helps us anticipate what will be needed from us.”
Starting off as technicians, assembling the different instruments, Marieta (who has been with the department for 27 years) and Disho (who has been there for 34 years) definitely have a good understanding of the inner workings of the MDRD.
“Yeah, we have a good idea of what’s going on, but even after these years, there’s still lots to know,” Marieta says smiling.
“I’ve put together a lot of instruments over the years,” Disho jumps in with a laugh. “I can’t remember all of that.”